Production technology
POCKET FILTER MANUFACTURING TECHNOLOGY
We use only top-quality filter materials from leading global manufacturers. These materials are processed on modern automated production lines in accordance with European standards EN ISO 16890.
Pocket Filter Production Using Sewing Technology – KSL Automatic Line
High-quality filter materials are prepared and cut to the required dimensions. The KSL automatic line employs advanced sewing technology to create pocket filters. This process involves precise stitching of individual layers to ensure strength and efficiency. Upon completion, filters undergo thorough quality control, checking seams, dimensions, and overall integrity to meet quality standards. Finished filters are carefully packed and prepared for distribution.
Pocket Filter Production Using Ultrasonic Welding
This method uses high-frequency ultrasonic waves to create strong, airtight bonds between filter material layers. These bonds ensure no particle leakage to the clean air side and offer high mechanical durability and long filter life.
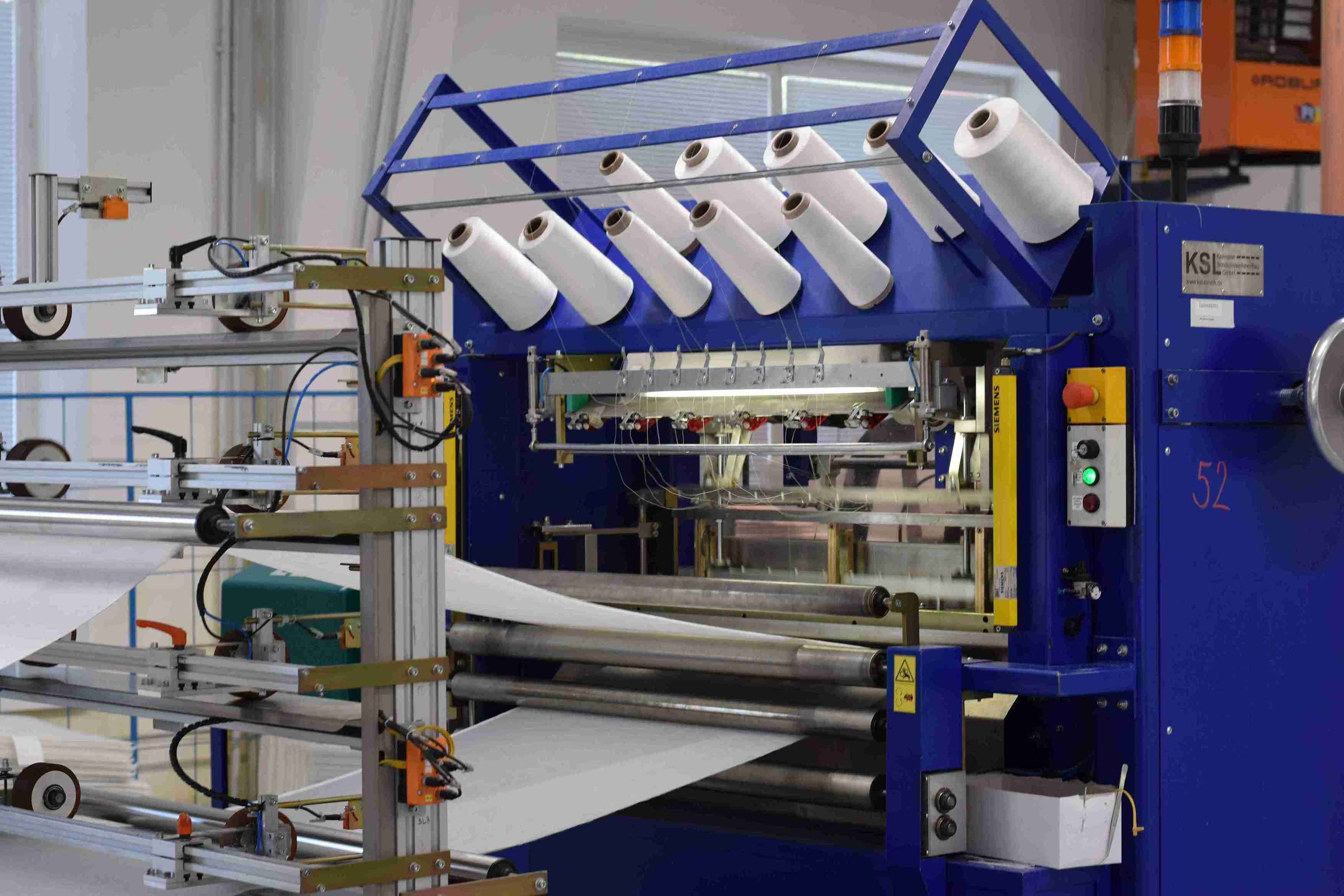
Pocket Filter Production Using Ultrasonic Welding
This method uses high-frequency ultrasonic waves to create strong, airtight bonds between filter material layers. These bonds ensure no particle leakage to the clean air side and offer high mechanical durability and long filter life.
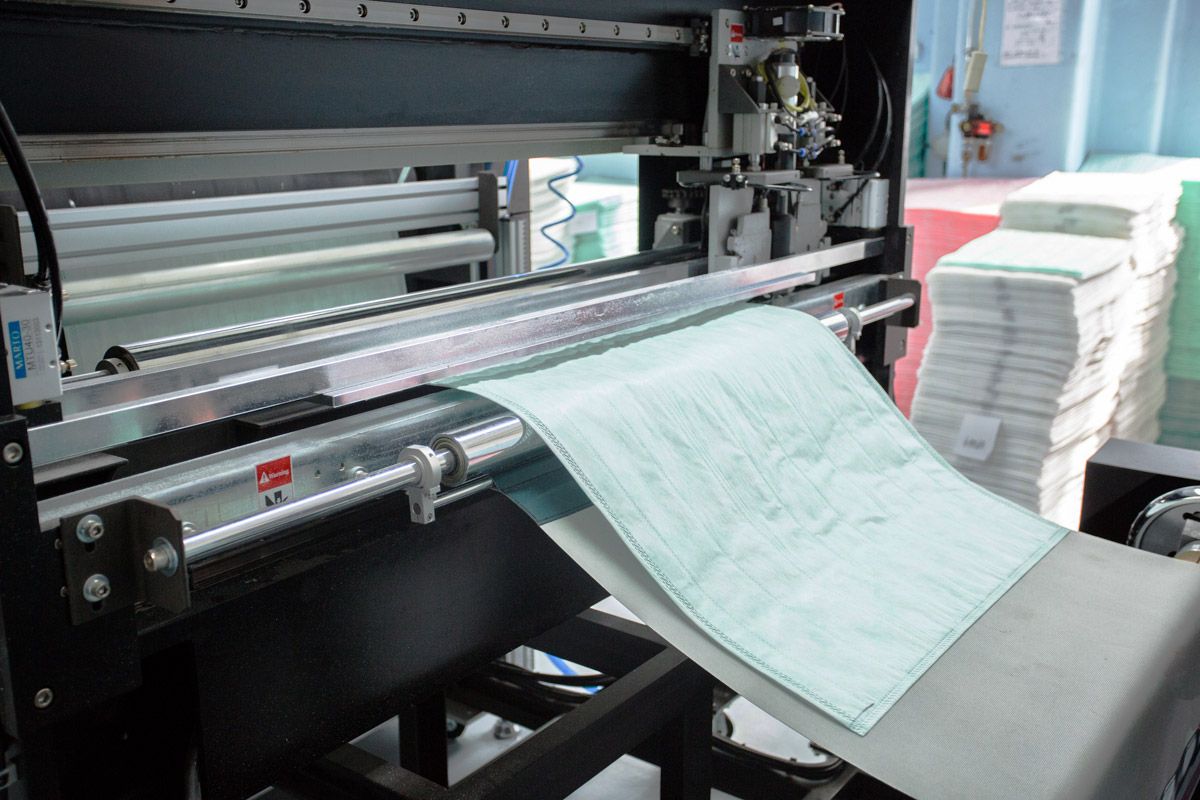
EPA, HEPA AND ULPA FILTER MANUFACTURING TECHNOLOGY
Minipleat and Panel Filter Folding Technology
The folding technology for minipleat and panel filters involves several key steps. First, the filter media is prepared—typically supplied in rolls and made from various types of fibers.
Using a specialized mechanism, the machine folds the prepared media into minipleats. This process creates regular pleats that increase the filter’s surface area and improve its efficiency.
After folding, the pleats are fixed in place using adhesive applied to the pleat edges. This step ensures the pleats remain stable and the filter retains its shape.
The finished minipleat packs are then cut to the required size, which may also include edge trimming to achieve precise dimensions.
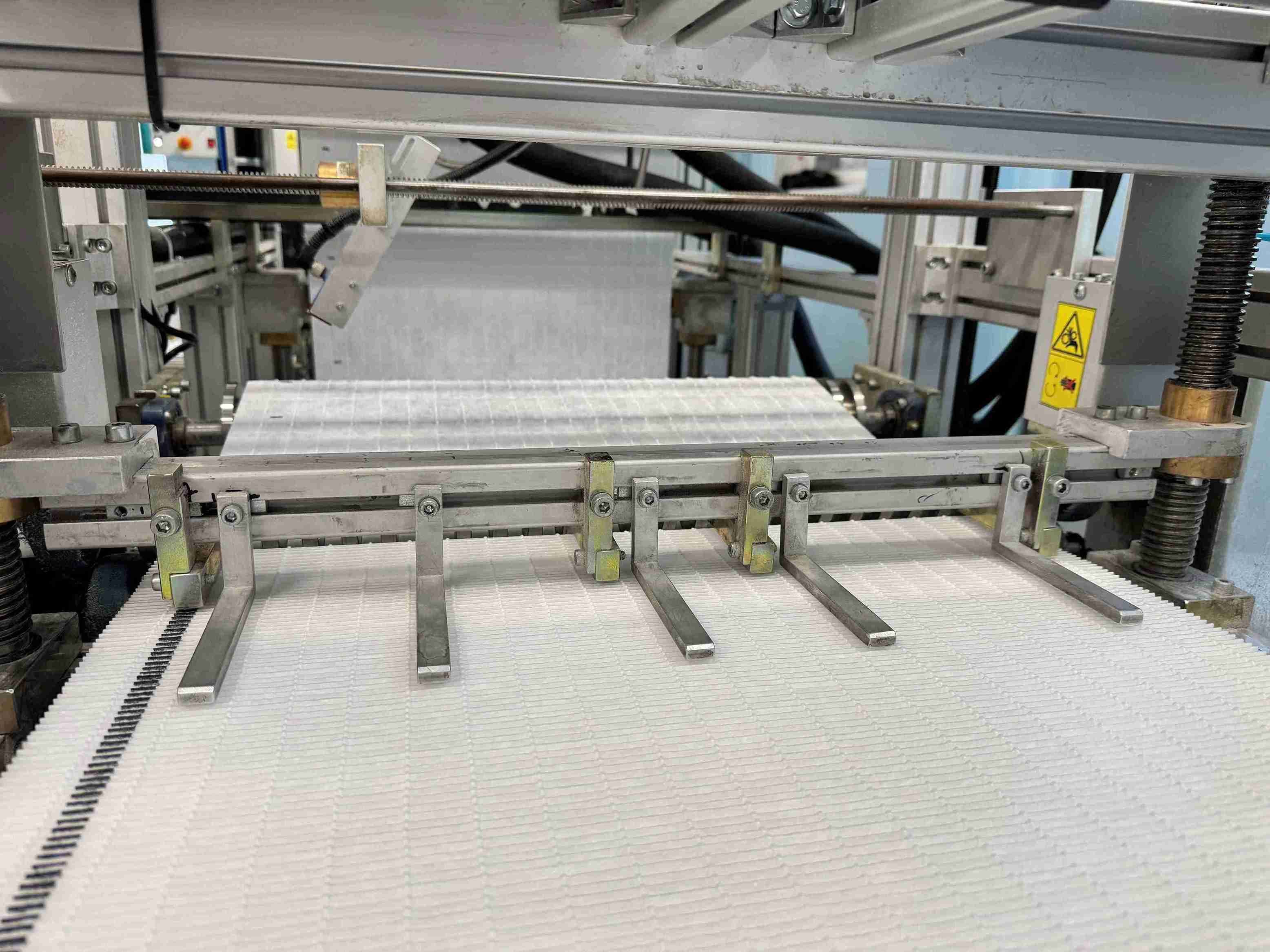
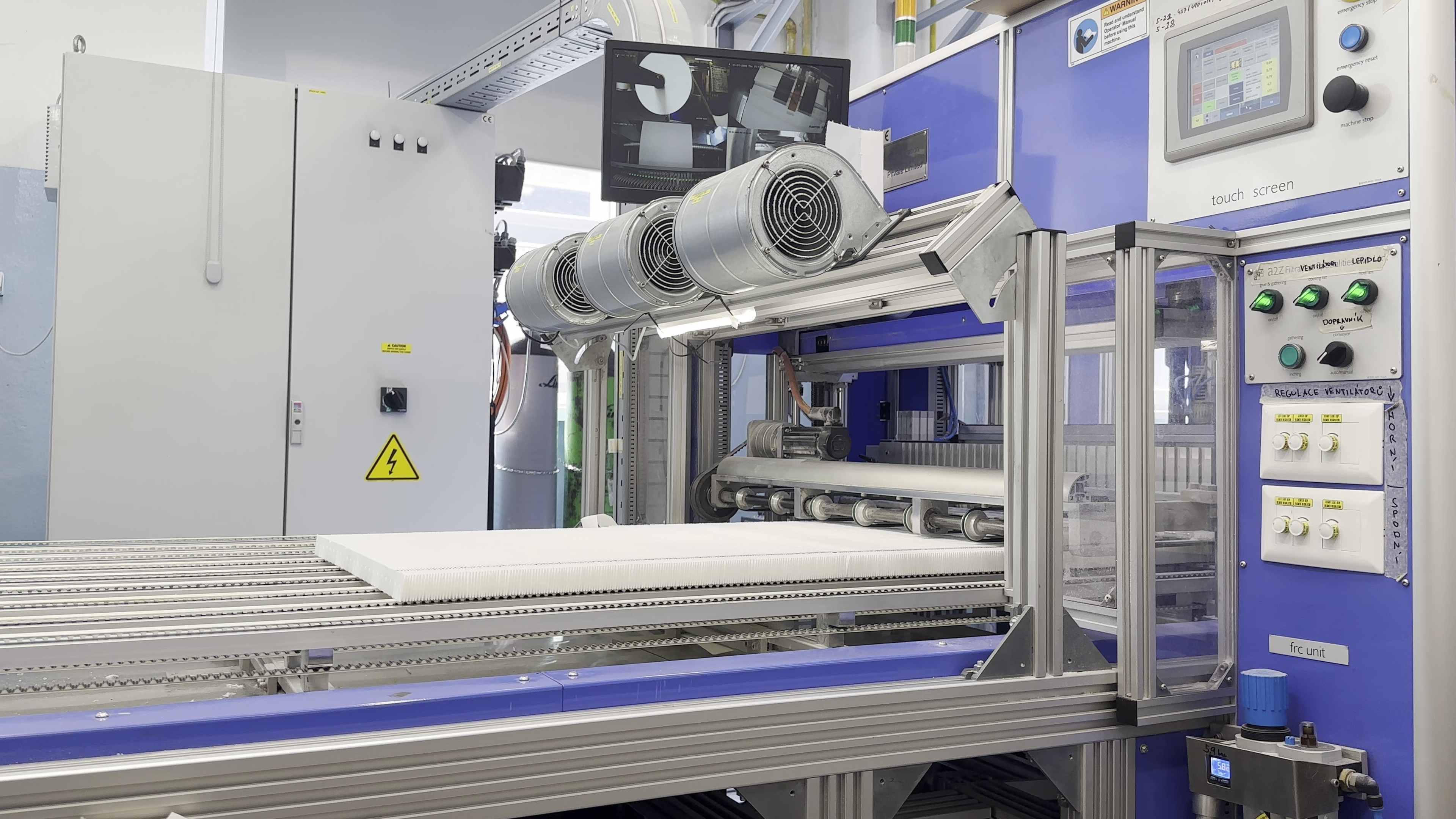
Each manufactured filter undergoes a quality control process to ensure it meets all required specifications and standards.
This thorough quality inspection is essential for ensuring the reliability and long service life of the filters. As a result, our customers can trust that our filters deliver optimal performance and protection in various applications—from industrial systems to critical environments where air cleanliness is vital.
EPA, HEPA, and ULPA Filter Manufacturing Technology
Potting Technology
Potting is a critical process in many industrial sectors where high quality and reliability of filtration systems are essential. In our production facilities, we use advanced technologies with a high level of automation.
The machines are designed to ensure high precision in the application of potting compounds (adhesives or sealants), providing even coverage and minimizing the risk of defects. The use of advanced technologies ensures a high-quality end product, with filters exhibiting excellent mechanical properties and long service life.
The potting process involves several steps. First, the individual filter components are prepared for the application of the potting compound. The machine then applies the compound with high precision and consistency—crucial for ensuring uniform coverage and reducing the likelihood of defects.
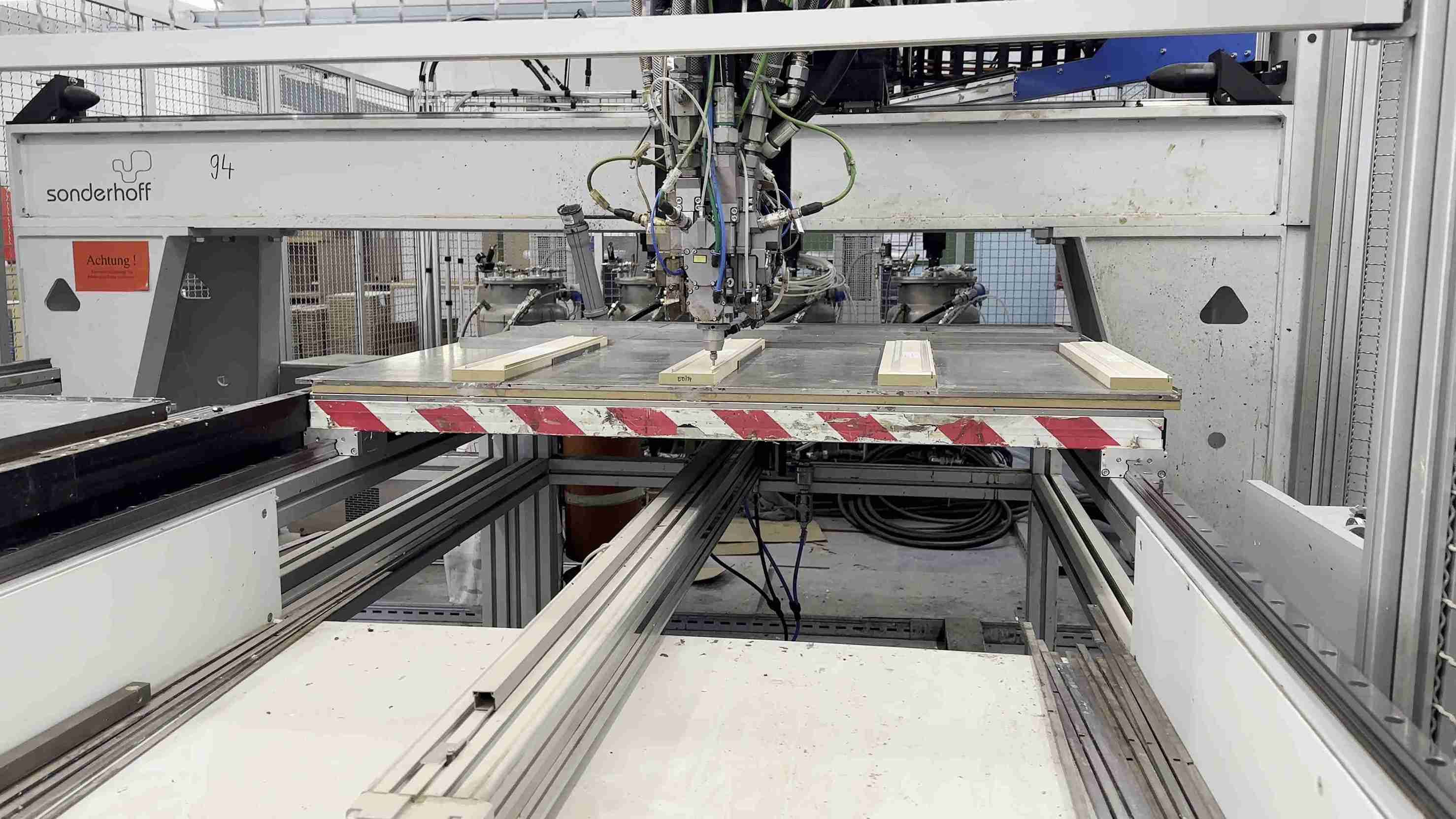
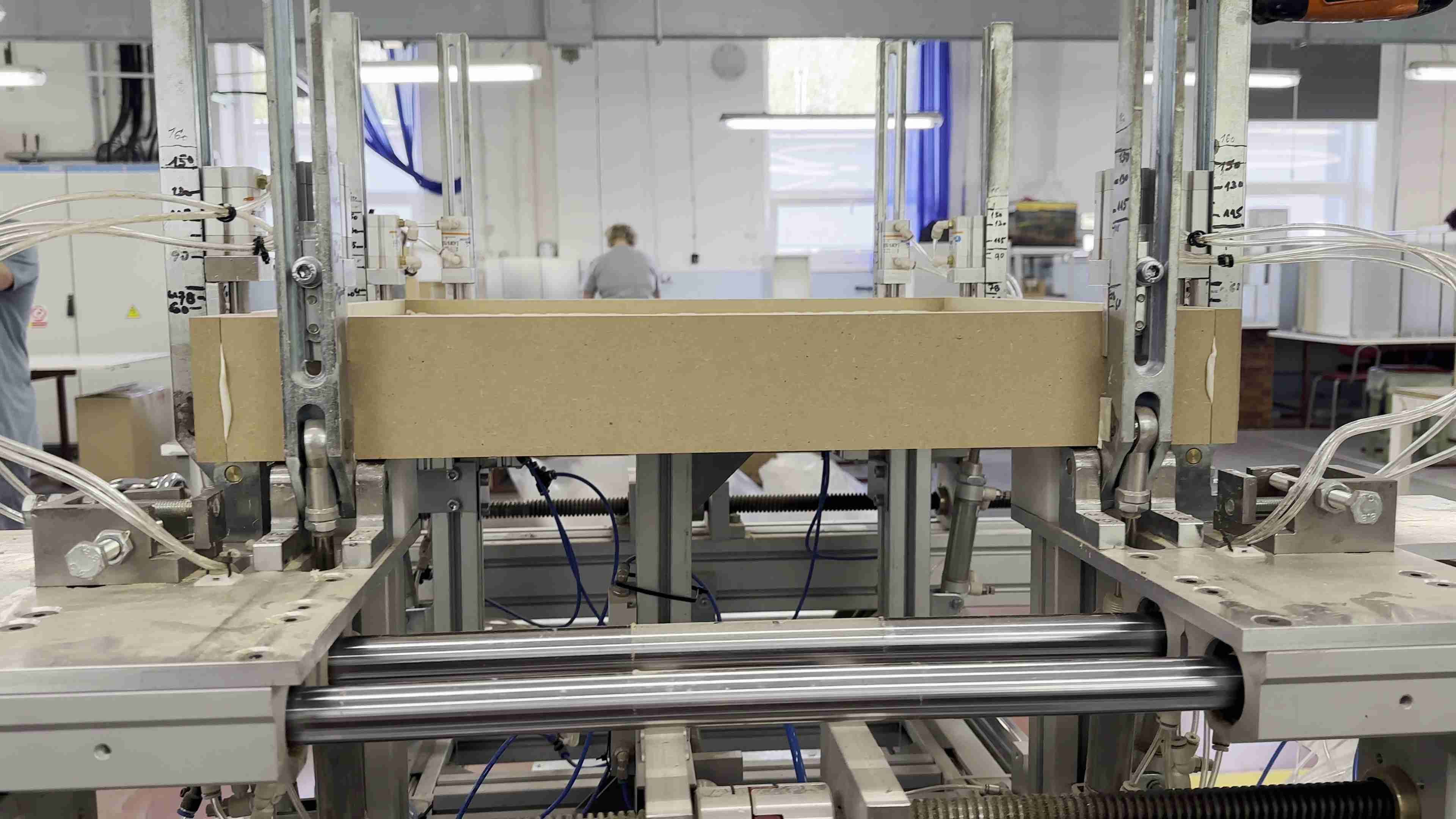
After the potting compound is applied, the final assembly of the filter follows. This step ensures that the compound achieves the required mechanical properties.
Each manufactured filter is then subjected to thorough quality control to verify that it meets all required specifications.
Z-LINE FILTER MANUFACTURING TECHNOLOGY
The production of Z-LINE filters involves several key steps to ensure high quality and filtration efficiency. This type of filter is popular for its simplicity, low weight, and effectiveness.
First, the filter media—usually supplied in rolls and made from various fiber types—is prepared and fed into a machine that folds it into the desired shape. This process forms uniform pleats, increasing the surface area and improving the filter’s performance.
After pleating, the media pack is inserted into a pre-designed frame that securely holds the filter media in place and ensures its stability. The pleats are then fixed to maintain their position, using either adhesive or thermal bonding. This step ensures the filter retains its shape and functionality.
Each finished filter undergoes rigorous quality control, including visual inspection, dimensional checks, and efficiency testing, to ensure it meets all required standards and specifications.
Thanks to advanced technology and careful quality assurance, our Z-LINE filters deliver high performance and reliability across a wide range of industrial applications.
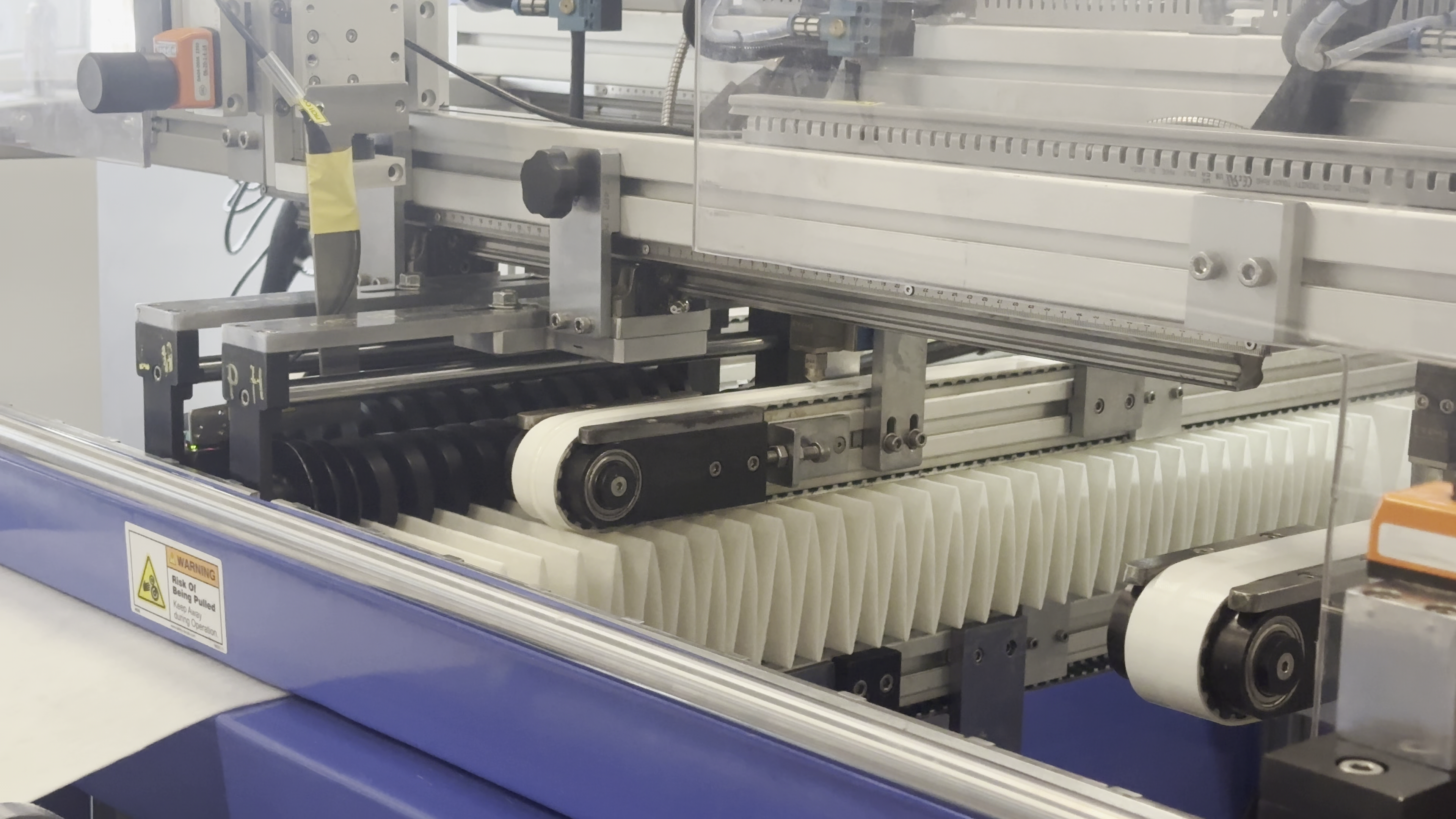
TECHNOLOGY FOR METAL FRAME PRODUCTION
Our production of metal filter frames uses advanced technologies to ensure high quality and precision for every component. In the production process, individual sheets are first cut to the required dimensions—a crucial step for accuracy and waste minimization. Laser cutting allows the creation of complex shapes and details with high precision and minimal risk of material deformation. The material is then formed into the desired frame shape using advanced pressing and forming tools, ensuring consistency and high quality.
The individual frame components are then welded together using automated welding systems, ensuring strength and structural stability. Each frame undergoes thorough quality control to meet all required standards and specifications. Finished frames are surface-treated, which may include painting, galvanizing, or other protective coatings. This treatment ensures corrosion resistance and extends the product’s lifespan.
Thanks to advanced technologies and automation, we achieve consistent production quality—essential for customer satisfaction.
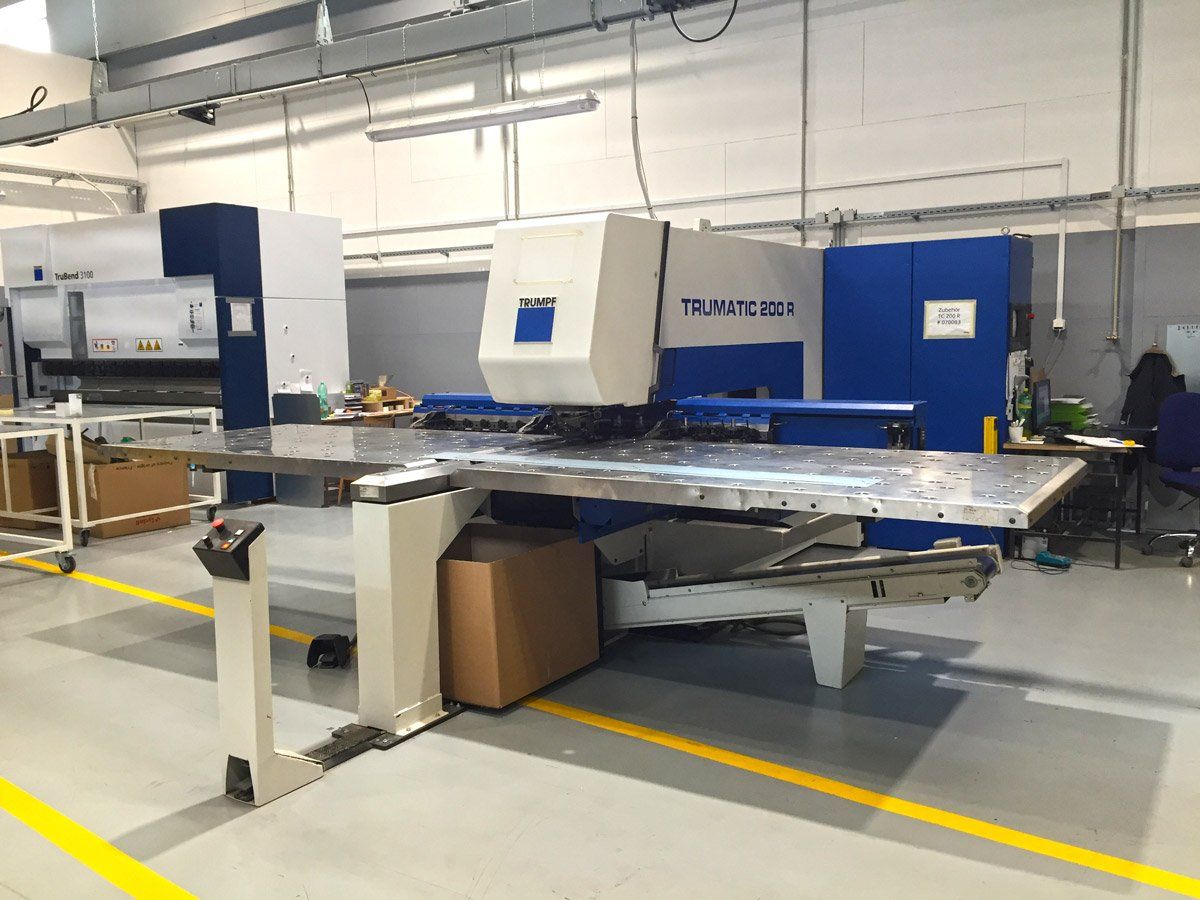
HIGH-PERFORMANCE MULTILAYER CUTTER
In our production process, we use a high-performance multilayer fabric cutter – a plotter. This advanced technology is designed for precise and efficient cutting of multilayer textiles. The machine uses cutting-edge systems that ensure a high level of accuracy and consistency.
The plotter is equipped with advanced sensors and control systems for precise cutting of complex shapes and patterns. The automation of the cutting process reduces human error and increases productivity. The machine is capable of working with multiple fabric layers at once, speeding up production and reducing material waste.
The plotter’s flexibility allows adaptation to different fabric types and filter designs. Its intuitive user interface ensures easy operation—even by less experienced operators.
The high-performance multilayer fabric cutter is an efficient solution for us, with a focus on precision, efficiency, and flexibility.
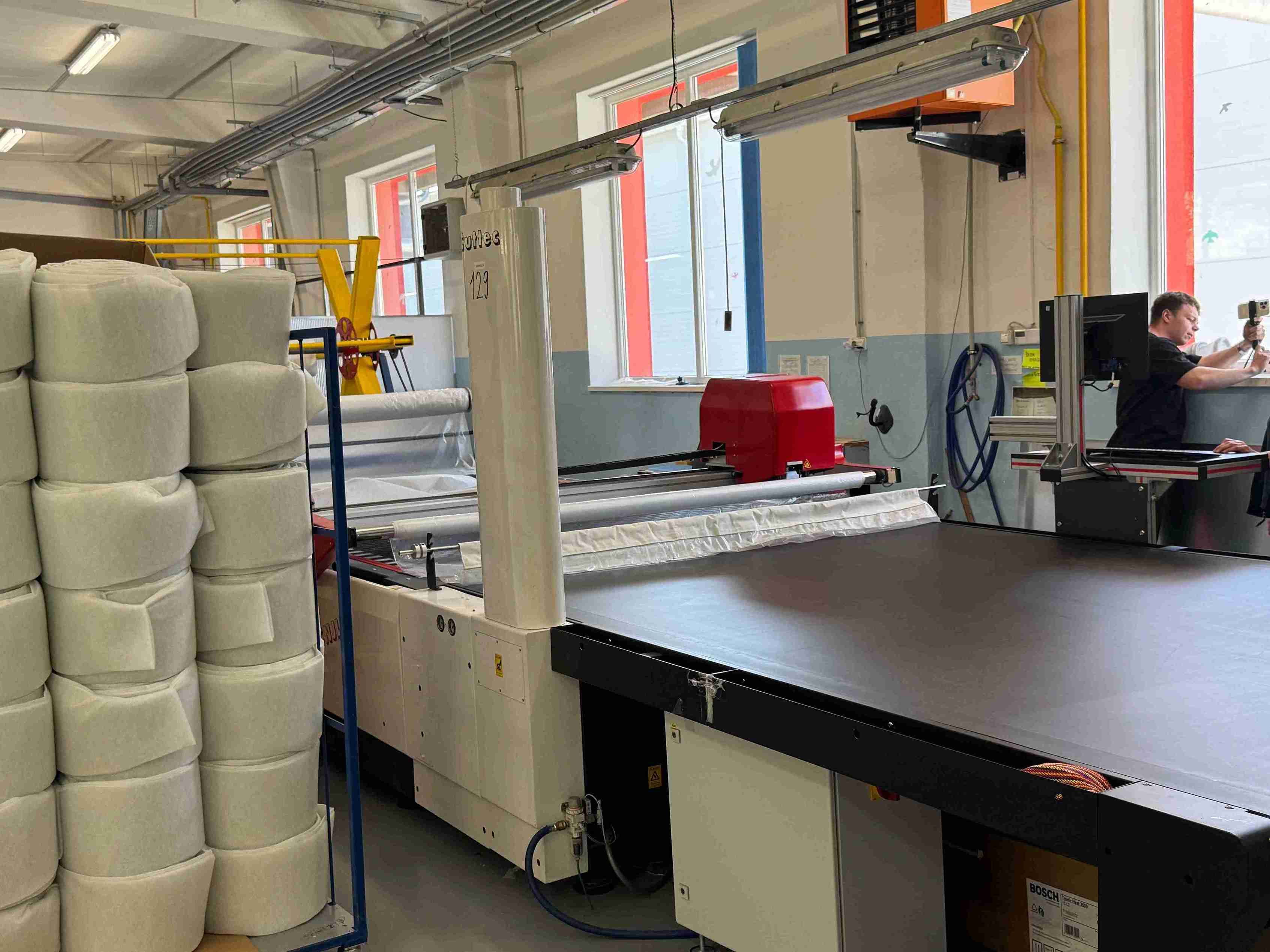