Technologie der Herstellung
Herstellungstechnologie von Taschenfiltern
Bei der Herstellung unserer Filter verwenden wir nur Filtermaterialien höchster Qualität von führenden Herstellern weltweit. Diese Materialien werden auf modernen automatisierten Fertigungslinien gemäß den europäischen Normen EN ISO 16890 verarbeitet.
Herstellung von Taschenfiltern mittels Nähtechnologie – automatische Linie KSL
Die hochwertigen Filtermaterialien werden vorbereitet und auf die gewünschten Maße zugeschnitten. Diese Materialien stammen in der Regel von renommierten internationalen Herstellern.
Die automatische KSL-Linie nutzt fortschrittliche Nähtechnologien zur Herstellung von Taschenfiltern. Dabei werden die einzelnen Lagen des Filtermaterials präzise vernäht, um deren Festigkeit und Filtrationseffizienz sicherzustellen.
Nach dem Nähvorgang durchlaufen die Filter eine gründliche Qualitätskontrolle, bei der insbesondere Nähte, Maße und die Gesamtkonstruktion überprüft werden. Ziel ist es, die Einhaltung aller relevanten Qualitätsnormen zu garantieren.
Die fertigen Filter werden sorgfältig verpackt und für den Versand an unsere Kunden vorbereitet.
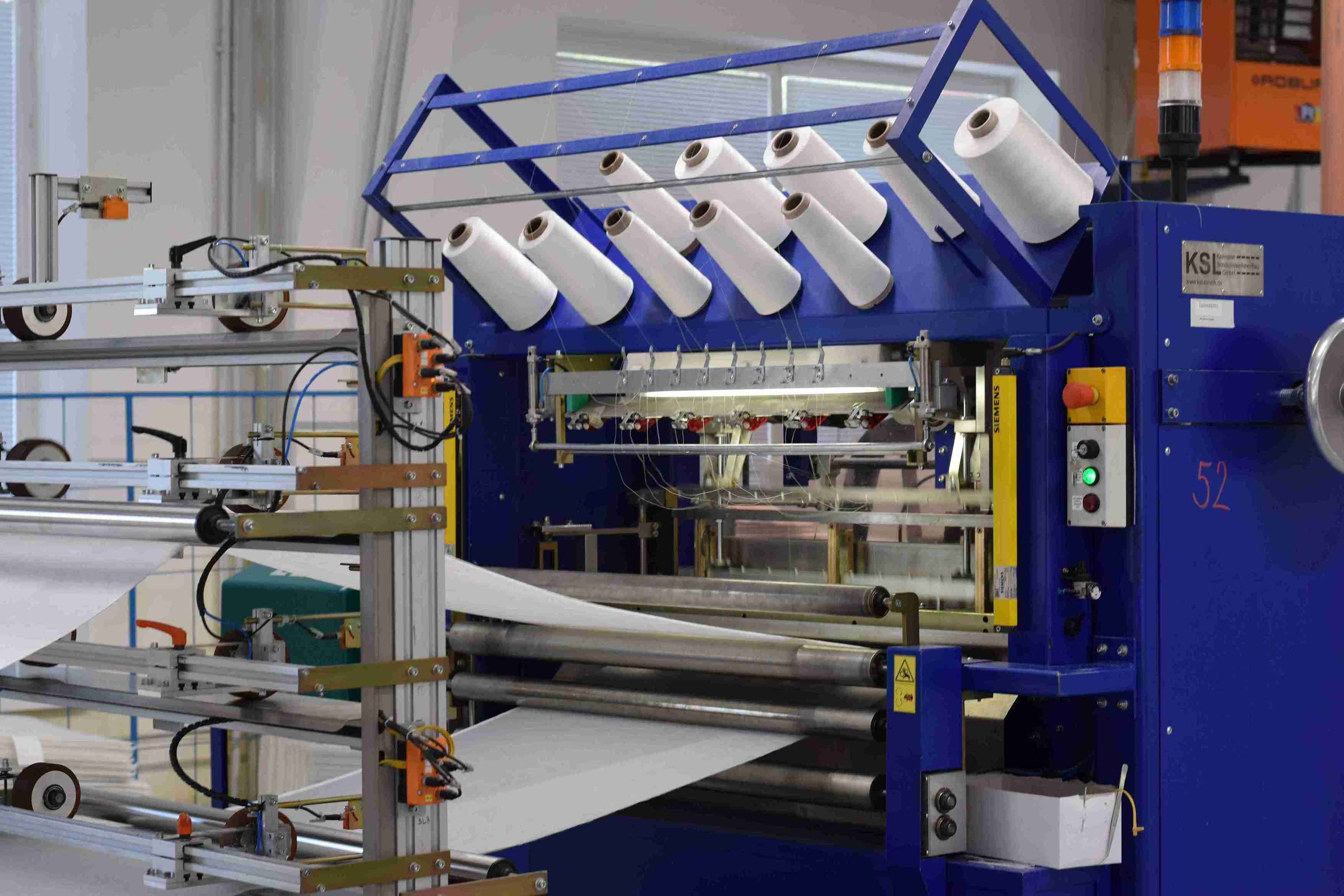
Herstellung von Taschenfiltern durch Ultraschallschweißen
Dieses Verfahren nutzt hochfrequente Ultraschallwellen, um starke und dichte Verbindungen zwischen den Schichten des Filtermaterials zu erzeugen. Die Ultraschallverbindungen gewährleisten die Integrität der Nähte ohne das Risiko eines Partikelaustritts auf die Reingasseite. Gleichzeitig sind diese festen und langlebigen Verbindungen widerstandsfähig gegenüber mechanischer Belastung und sorgen für eine lange Lebensdauer der Filter.
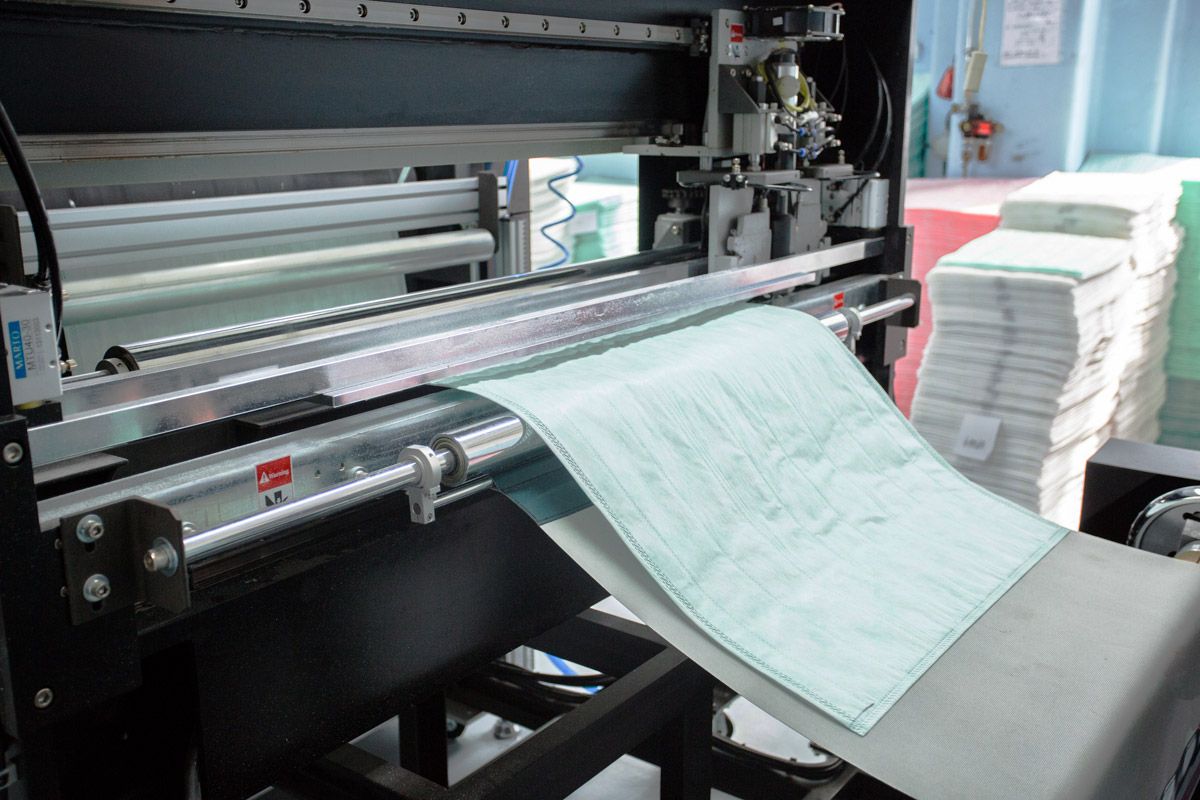
Herstellungstechnologie von EPA-, HEPA- und ULPA-Filtern
Minipleat- und Paneelfilter-Falttechnologie
Die Falttechnologie für Minipleat- und Paneelfilter umfasst mehrere entscheidende Schritte. Zunächst wird das Filtermaterial vorbereitet – in der Regel in Rollenform – und kann aus verschiedenen Faserarten bestehen.
Mithilfe eines speziellen Mechanismus wird das vorbereitete Material zu gleichmäßigen Minifalten (Minipleats) geformt. Dieser Prozess erhöht die Oberfläche des Filters und verbessert seine Filtrationseffizienz.
Nach dem Falten werden die Falten mit einem Klebstoff fixiert, der auf die Kanten der Falten aufgetragen wird. Dieser Schritt stellt sicher, dass die Falten stabil bleiben und der Filter seine Form behält.
Die fertigen Minipleats werden anschließend auf die gewünschte Größe zugeschnitten, was auch das Trimmen der Kanten zur Erreichung exakter Abmessungen beinhalten kann.
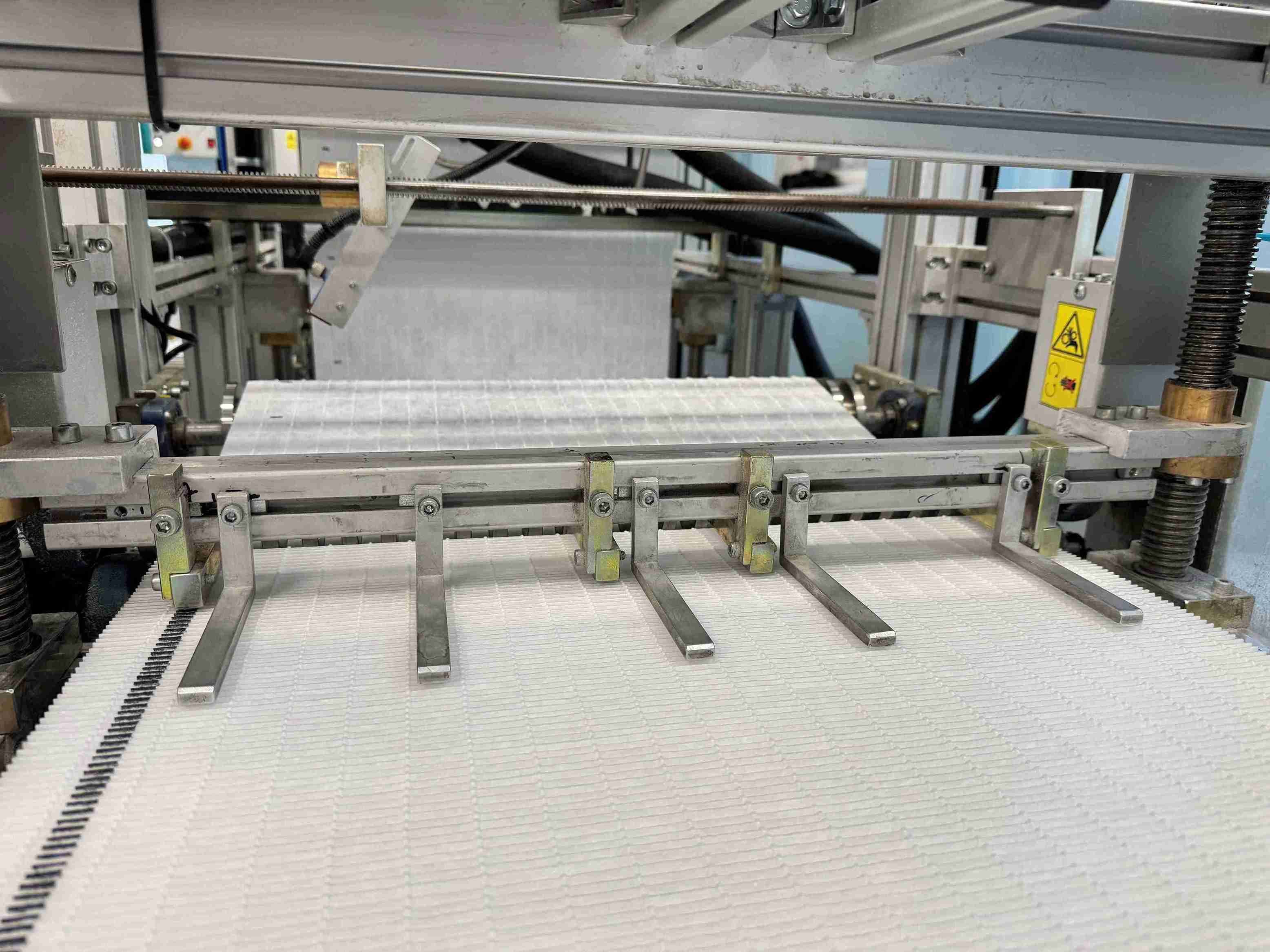
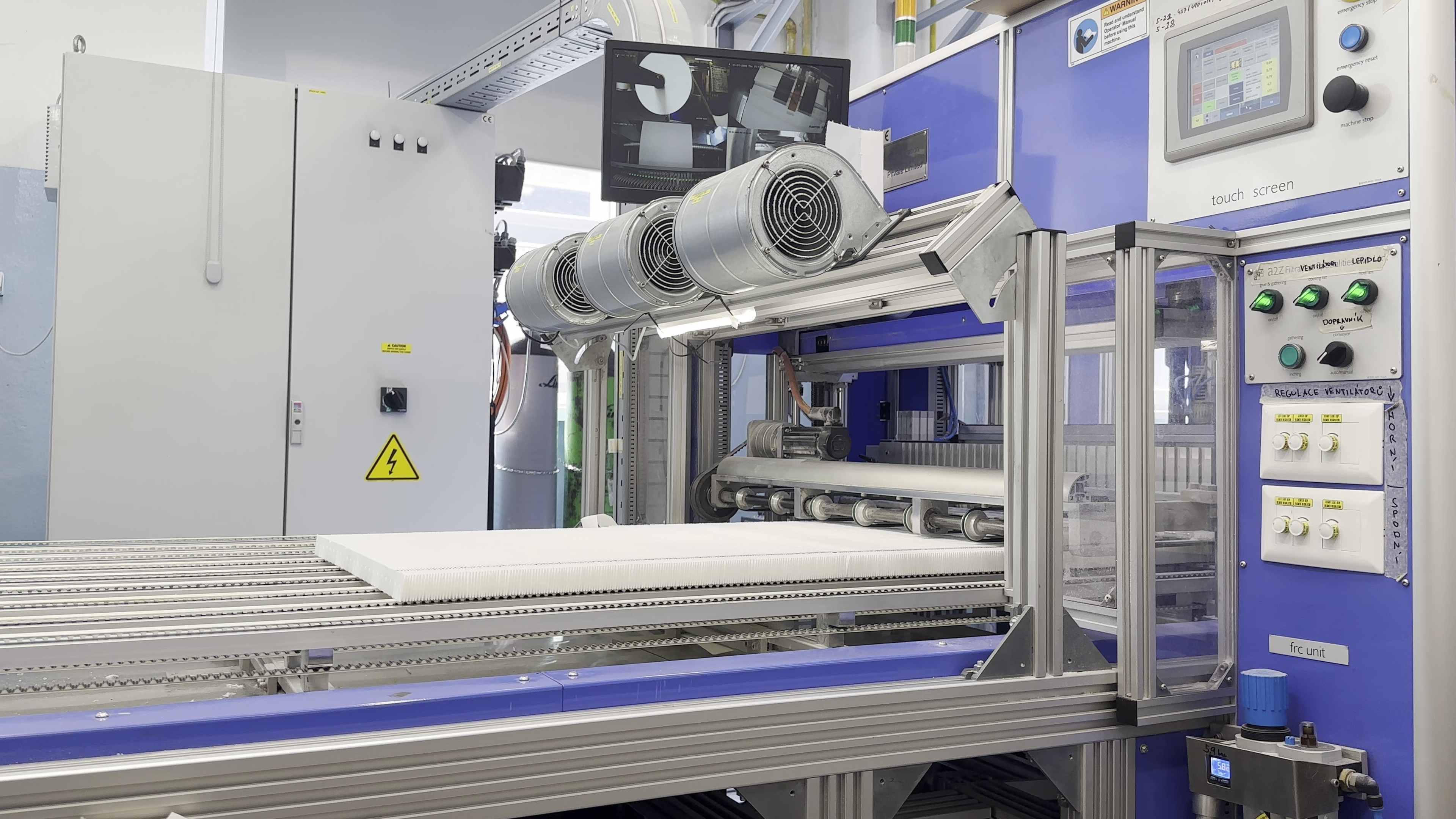
Jeder hergestellte Filter durchläuft eine Qualitätskontrolle, um sicherzustellen, dass er alle erforderlichen Spezifikationen und Normen erfüllt.¨
Dieser gründliche Qualitätsprüfprozess ist entscheidend für die Zuverlässigkeit und lange Lebensdauer der Filter.
So können unsere Kunden darauf vertrauen, dass unsere Filter eine optimale Leistung und Schutz in unterschiedlichsten Anwendungen bieten – von industriellen Systemen bis hin zu kritischen Bereichen, in denen Luftreinheit von entscheidender Bedeutung ist.
Herstellungstechnologie von EPA-, HEPA- und ULPA-Filtern
Vergusstechnologie
Das Vergießen von Filtern ist ein entscheidender Prozess in vielen Industriebranchen, in denen hohe Qualität und Zuverlässigkeit der Filtersysteme erforderlich sind. In unserem Produktionsbereich setzen wir fortschrittliche Technologien mit einem hohen Automatisierungsgrad ein.
Die Maschinen sind so konzipiert, dass sie eine hohe Präzision bei der Applikation der Vergussmasse (Klebstoff oder Dichtmittel) gewährleisten. Dies sorgt für eine gleichmäßige Abdeckung und minimiert das Risiko von Defekten. Der Einsatz moderner Technologien stellt eine hohe Qualität des Endprodukts sicher – die Filter zeichnen sich durch hervorragende mechanische Eigenschaften und eine lange Lebensdauer aus.
Der Vergussprozess umfasst mehrere Schritte. Zunächst werden die einzelnen Filterkomponenten für die Applikation der Vergussmasse vorbereitet. Anschließend trägt die Maschine die Masse mit hoher Genauigkeit und Konsistenz auf – ein entscheidender Faktor für eine gleichmäßige Abdeckung und die Vermeidung von Fehlern.
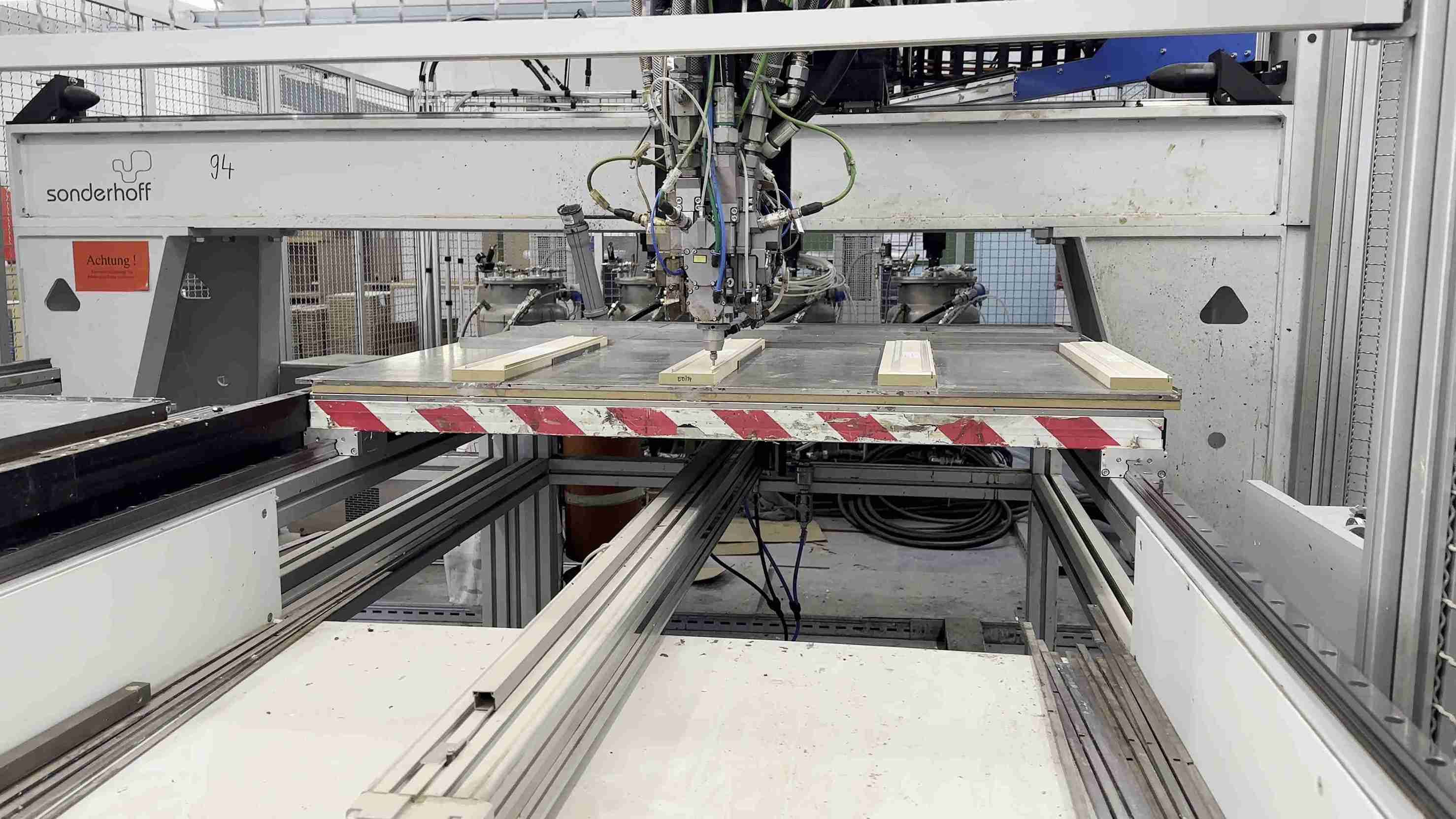
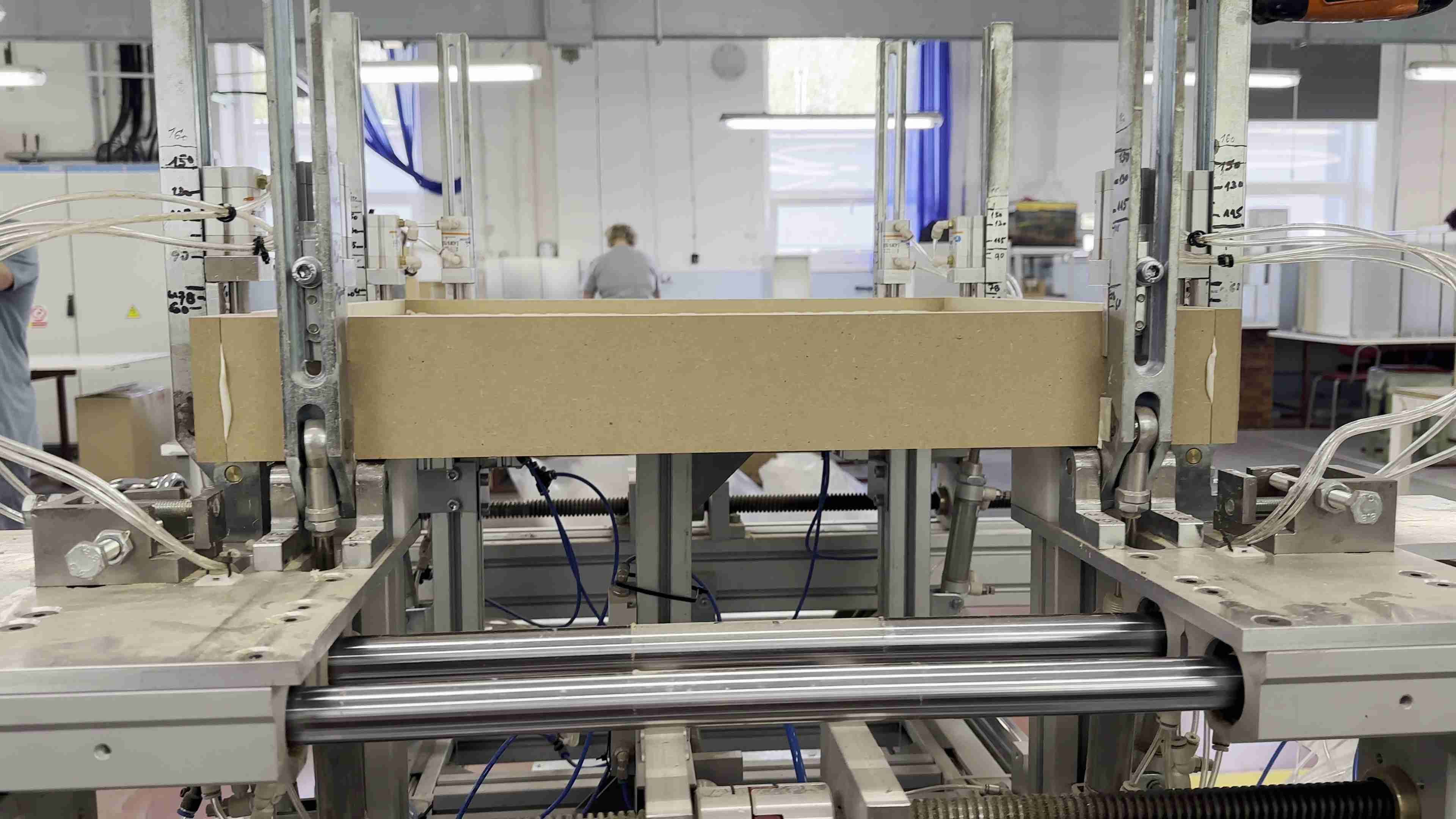
Nach dem Auftragen der Vergussmasse folgt der Zusammenbau des fertigen Filters, wodurch sichergestellt wird, dass die Masse die gewünschten mechanischen Eigenschaften erreicht.
Jeder hergestellte Filter wird anschließend einer gründlichen Qualitätskontrolle unterzogen, um sicherzustellen, dass er alle erforderlichen Spezifikationen erfüllt.
Herstellungstechnologie für Z-LINE-Filter
Die Herstellung von Z-LINE-Filtern ist ein Prozess, der mehrere entscheidende Schritte umfasst, um eine hohe Qualität und Effizienz der Filtersysteme sicherzustellen. Dieser Filtertyp ist beliebt aufgrund seiner Einfachheit, seines geringen Gewichts und seiner hohen Leistungsfähigkeit.
Zunächst wird das Filtermaterial vorbereitet – in der Regel in Rollenform – und kann aus verschiedenen Faserarten bestehen. Anschließend wird das Material in eine Maschine geführt, die es in die gewünschte Form faltet. Dabei entstehen gleichmäßige, regelmäßige Falten, welche die Oberfläche des Filters vergrößern und somit seine Filterleistung verbessern.
Nach der Faltung wird das Filterpaket in einen vorgefertigten Rahmen eingesetzt. Der Rahmen ist so konzipiert, dass er das Filtermaterial sicher an seinem Platz hält und dessen Stabilität gewährleistet. Die Falten des Filtermaterials werden fixiert, um ihre Position zu bewahren – dieser Schritt kann Klebstoff oder eine thermische Behandlung beinhalten, um sicherzustellen, dass der Filter seine Form und Funktion behält.
Jeder hergestellte Filter wird einer sorgfältigen Qualitätskontrolle unterzogen, um sicherzustellen, dass er alle erforderlichen Spezifikationen und Normen erfüllt. Dieser Prozess beinhaltet eine visuelle Inspektion, Maßkontrolle und die Prüfung der Filtereffizienz.
Die Herstellung von Z-LINE-Filtern ist ein komplexer Prozess mit mehreren wichtigen Schritten. Dank modernster Technologien und strenger Qualitätskontrollen sind unsere Filter in der Lage, hohe Effizienz und Zuverlässigkeit in verschiedensten industriellen Anwendungen zu bieten. So stellen wir sicher, dass jeder Filter alle erforderlichen Standards erfüllt und seine Funktion zuverlässig erfüllt.
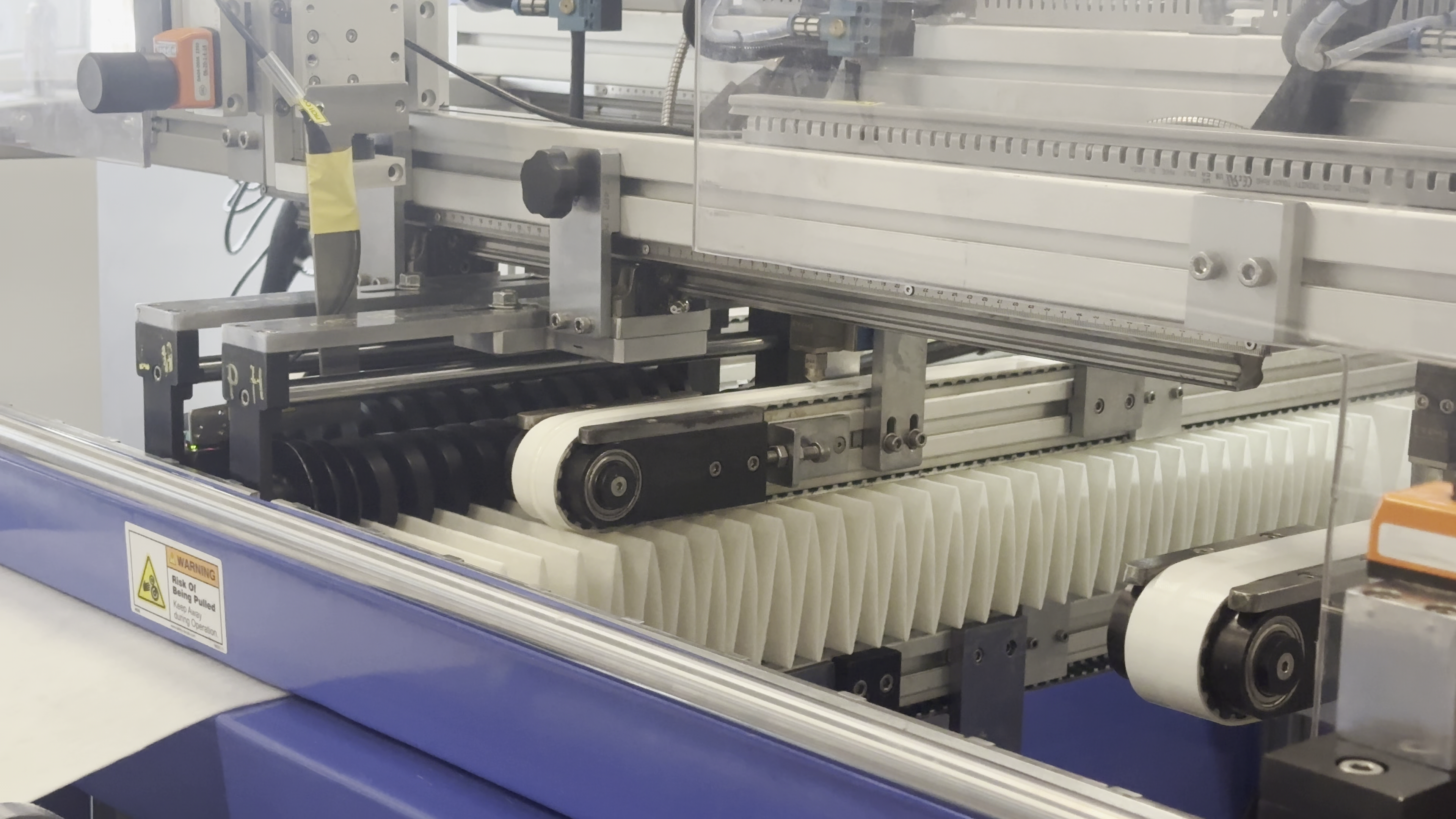
Herstellungstechnologie für Metallrahmen
Unsere Produktion von Metallrahmen für Filter nutzt fortschrittliche Technologien, um eine hohe Qualität und Präzision jedes einzelnen Bauteils sicherzustellen. Im Rahmen des Fertigungsprozesses werden zunächst die Blechzuschnitte auf die gewünschten Maße gebracht. Dieser Schritt ist entscheidend, um Genauigkeit zu gewährleisten und Materialabfall zu minimieren. Das Laserschneiden ermöglicht die Herstellung komplexer Formen und Details mit hoher Präzision und minimalem Risiko der Materialverformung. Anschließend wird das Material in die gewünschte Rahmenform gebracht. Dank moderner Stanz- und Umformwerkzeuge erzielen wir eine gleichbleibend hohe Qualität und Maßhaltigkeit der Endprodukte.
Die einzelnen Rahmenteile werden anschließend mithilfe automatisierter Schweißsysteme miteinander verbunden, was für die Festigkeit und Stabilität des Rahmens sorgt. Jeder Rahmen durchläuft eine gründliche Qualitätskontrolle, um sicherzustellen, dass er alle vorgeschriebenen Normen und Spezifikationen erfüllt.
Die fertigen Rahmen werden anschließend oberflächenbehandelt – durch Lackierung, Verzinkung oder andere Schutzbeschichtungen. Diese Behandlung schützt die Rahmen zuverlässig vor Korrosion und verlängert ihre Lebensdauer.
Dank fortschrittlicher Technologien und automatisierter Anlagen erreichen wir eine gleichbleibend hohe Produktionsqualität – ein entscheidender Faktor für die Zufriedenheit unserer Kunden.
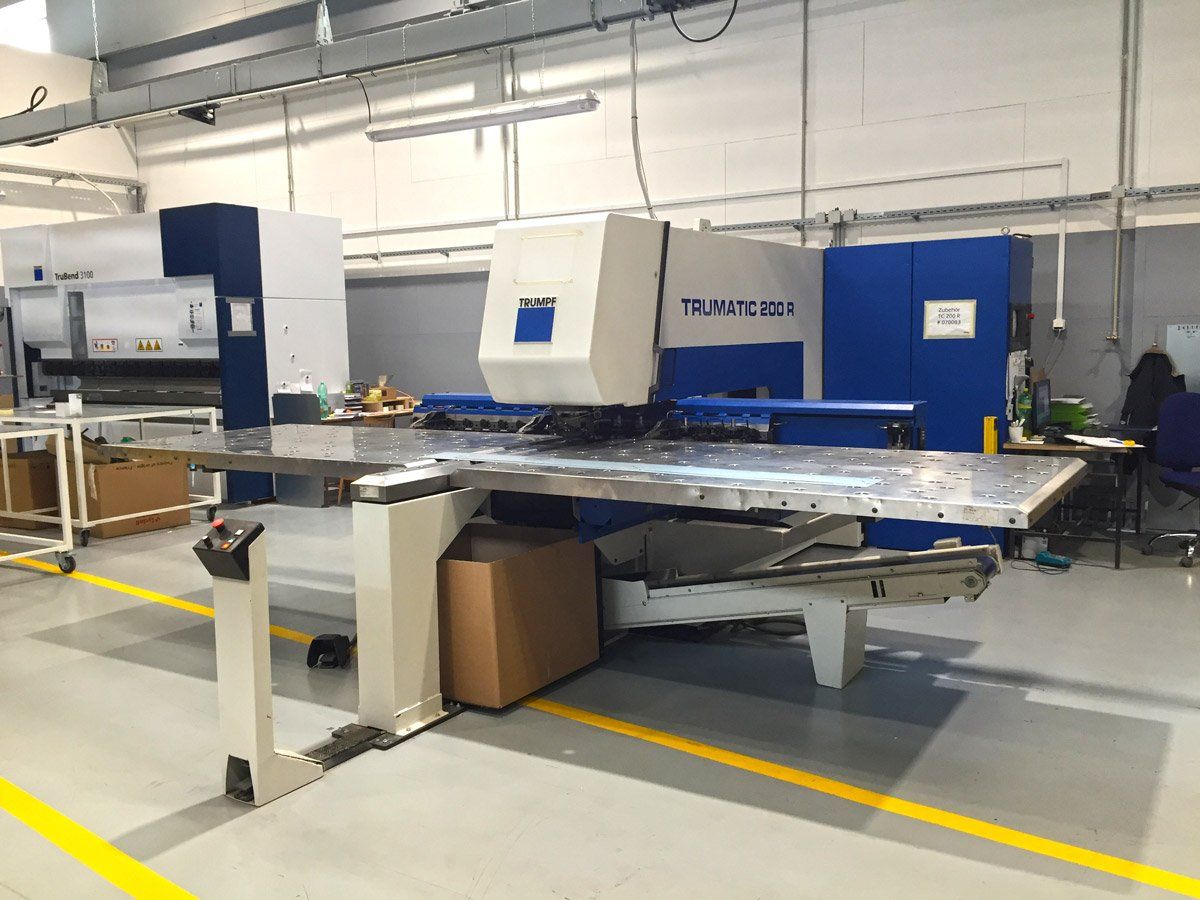
Hochleistungs-Mehrlagen-Schneideanlage
In unserem Produktionsprozess setzen wir einen leistungsstarken Mehrlagen-Stoffschneider – einen Plotter – ein. Diese moderne Technologie ist für das präzise und effiziente Schneiden mehrlagiger Textilien konzipiert. Die Maschine nutzt fortschrittliche Technologien, die eine hohe Genauigkeit und Konsistenz beim Schneiden gewährleisten.
Der Plotter ist mit modernen Sensoren und Steuerungssystemen ausgestattet, die das präzise Schneiden komplexer Formen und Muster ermöglichen. Die Automatisierung des Schneidprozesses minimiert menschliche Fehler und erhöht die Produktivität. Die Maschine kann mehrere Stofflagen gleichzeitig bearbeiten, was den Produktionsprozess beschleunigt und den Materialabfall reduziert.
Die Flexibilität des Plotters erlaubt die Anpassung an verschiedene Stoff- und Filtertypen. Die benutzerfreundliche Oberfläche sorgt für eine einfache Bedienung, auch durch weniger erfahrene Bediener.
Der hochleistungsfähige Mehrlagen-Stoffschneider stellt für uns eine effiziente Lösung dar – mit Fokus auf Präzision, Effizienz und Flexibilität.
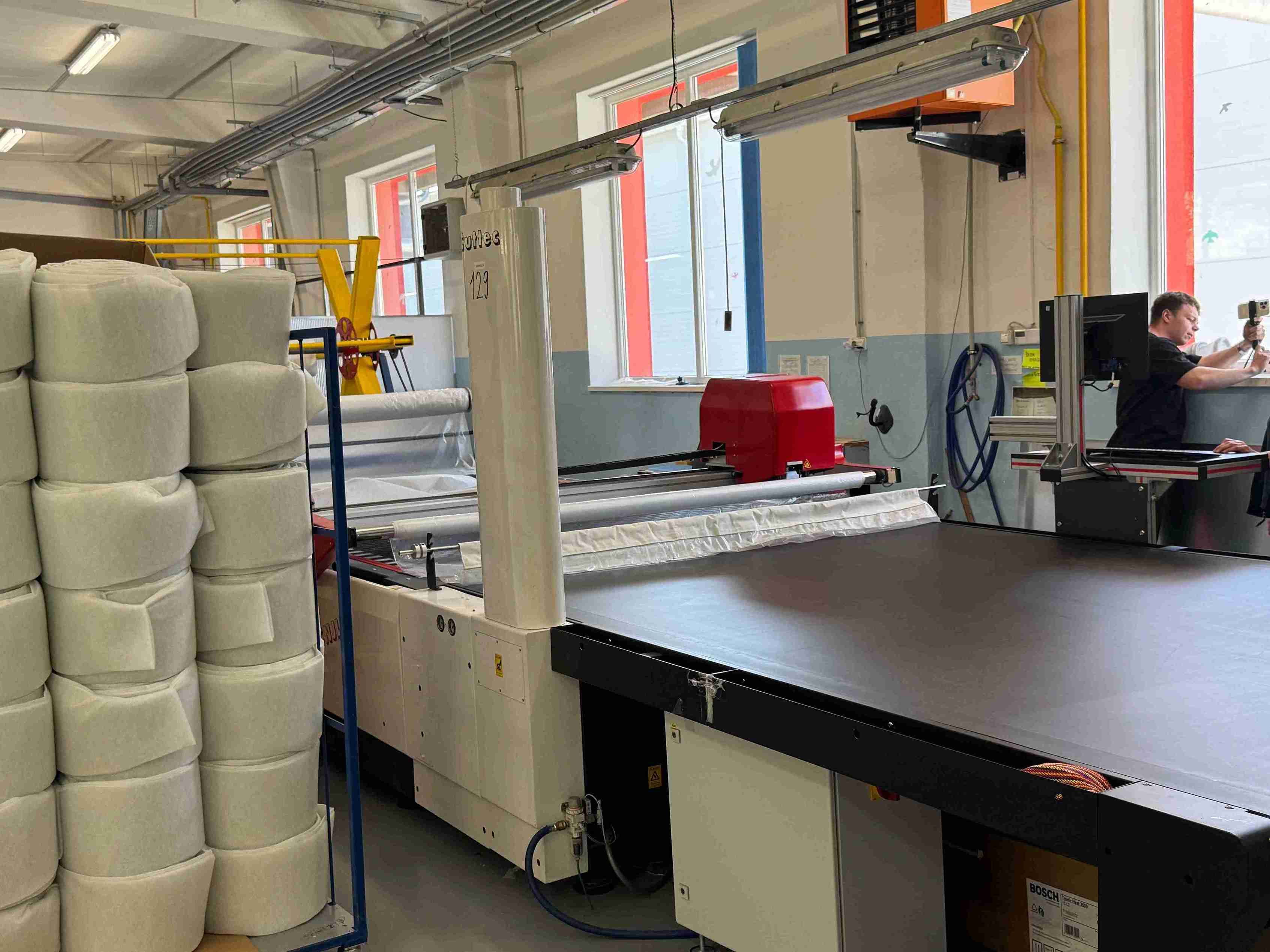